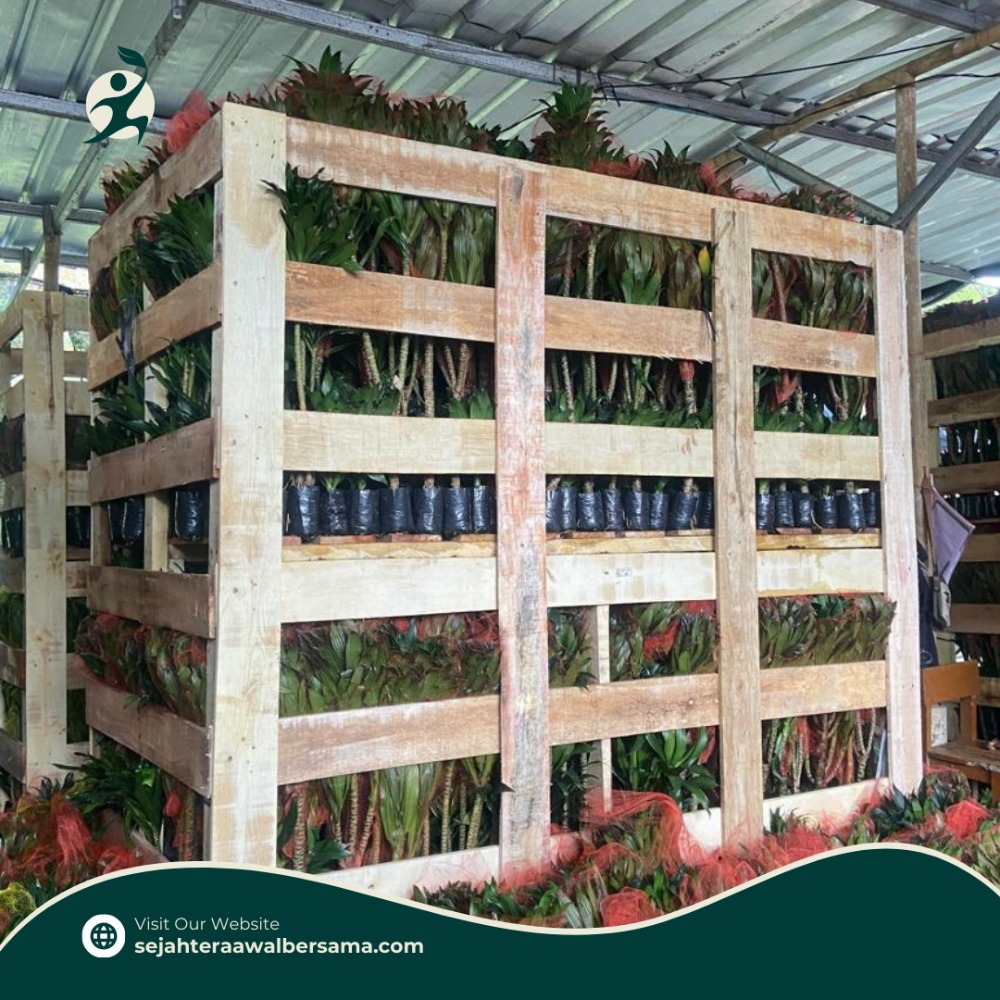
In the global marketplace, ensuring the quality of products from export plants like Compacta is essential for maintaining customer satisfaction, meeting regulatory standards, and enhancing brand reputation. This article delves into the critical aspects of quality assurance in Compacta's export plant operations and outlines effective strategies to achieve and sustain high-quality standards.
1. Implementing Standard Operating Procedures (SOPs)
Standard Operating Procedures (SOPs) are foundational to maintaining consistent quality in Compacta’s production processes. They ensure that every task is performed correctly and uniformly, reducing variability and errors.
Strategies:
Comprehensive Documentation: Develop detailed SOPs for all stages of the production process, from raw material handling to final packaging.
Employee Training: Conduct regular training sessions to ensure all employees are familiar with and adhere to the SOPs.
Regular Updates: Periodically review and update SOPs to incorporate new best practices and technological advancements.
2. Employee Training and Development
A knowledgeable and skilled workforce is crucial for maintaining quality standards. At Compacta, investing in employee training and development ensures that staff are competent and motivated to uphold quality in their work.
Strategies:
Continuous Learning: Implement continuous training programs to keep employees updated on the latest industry practices and technologies.
Quality Culture: Promote a culture of quality where every employee understands their role in achieving and maintaining high standards.
Skill Enhancement: Provide opportunities for skill development and advanced training to foster expertise in quality management.
3. Robust Quality Control Systems
Quality control systems are essential for detecting defects and ensuring that products meet the desired quality standards before they reach customers.
Strategies:
Regular Inspections: Conduct inspections at critical stages of the production process to identify and address defects early.
Advanced Testing: Use state-of-the-art testing methods to ensure the quality of raw materials and finished products.
Automated Quality Control: Incorporate automated quality control systems to increase precision and efficiency in detecting defects
4. Supplier Quality Management
The quality of raw materials and components significantly affects the final product. Ensuring that suppliers meet Compacta’s quality standards is crucial for maintaining overall product quality.
Strategies:
Supplier Audits: Perform regular audits of suppliers to verify their adherence to quality requirements.
Collaborative Relationships: Build strong relationships with suppliers to encourage cooperation and continuous improvement.
Performance Tracking: Monitor supplier performance through metrics and provide feedback to drive quality enhancements.
5. Continuous Improvement Programs
Continuous improvement is vital for sustaining high-quality standards over time. It involves regularly evaluating and improving processes to enhance efficiency and effectiveness.
Strategies:
Kaizen Principles: Apply Kaizen principles to foster a culture of ongoing, incremental improvements.
Lean Manufacturing: Adopt lean manufacturing techniques to minimize waste and optimize production processes.
Feedback Mechanisms: Establish mechanisms to collect and act on feedback from employees and customers to drive continuous improvement.
6. Regular Quality Audits
Quality audits help assess the effectiveness of Compacta’s quality management system and identify areas for improvement.
Strategies:
Internal Audits: Conduct regular internal audits to ensure compliance with established quality standards.
External Audits: Engage external auditors to provide an impartial evaluation of the quality management system.
Corrective Actions: Implement corrective actions based on audit findings to address any identified issues promptly.
7. Customer Feedback and Satisfaction
Customer feedback is invaluable for understanding the quality of Compacta’s products and identifying areas for enhancement.
Strategies:
Customer Surveys: Regularly conduct surveys to gather customer feedback on product quality and satisfaction.
Complaint Resolution: Establish a robust system for managing and resolving customer complaints efficiently.
Product Refinement: Use insights from customer feedback to refine products and improve quality continually.
Ensuring quality in Compacta’s export plant operations is a comprehensive endeavor that involves meticulous planning, continuous training, robust quality control systems, and a commitment to continuous improvement. By implementing these strategies, Compacta can consistently deliver high-quality products that meet international standards, satisfy customers, and strengthen its competitive position in the global market.